Recent reports suggest as many as 20 billion devices could be connected to the Industrial Internet of Things (IIoT) in a market potentially worth over $200 billion within a few years.
For manufacturers keen to ensure their production facilities remain competitive, they will need to embrace the IioT (Industrial Internet of Things) where the physical world is connected to the digital via Smart Sensors.
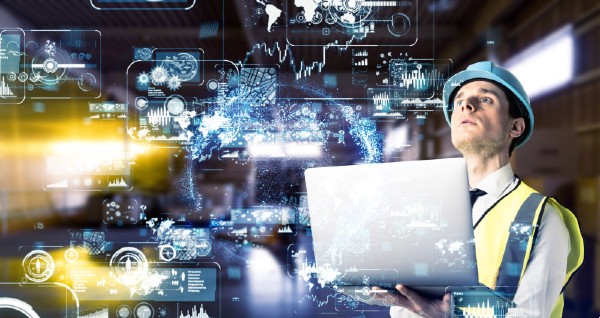
These Smart Sensors, that sense, measure, process, interpret and connect to the digital world is the technology that is being embraced across industry. All of these functions can be integrated into a mixed signal Application Specific Integrated Circuit (ASIC) or a System in Package (SiP) solution providing a genuine cost and performance enhancement for the smart sensor over traditional discrete component level solutions.
ASICs and SiPs Increasingly Found in Industrial Applications
The term ASIC was historically associated with the type of high-volume applications found in automotive and consumer electronics for example. However, by combining the latest design techniques with today’s chip manufacturing and packaging technology, ASICs and SiPs are increasingly found in industrial applications and one of the fastest growing of these is the Industrial Internet of Things (IIoT) or the so-called Smart Sensor, where the latest electronics technology is enhancing manufacturing techniques along with assisting plant managers to control and monitor their facility’s overall performance.
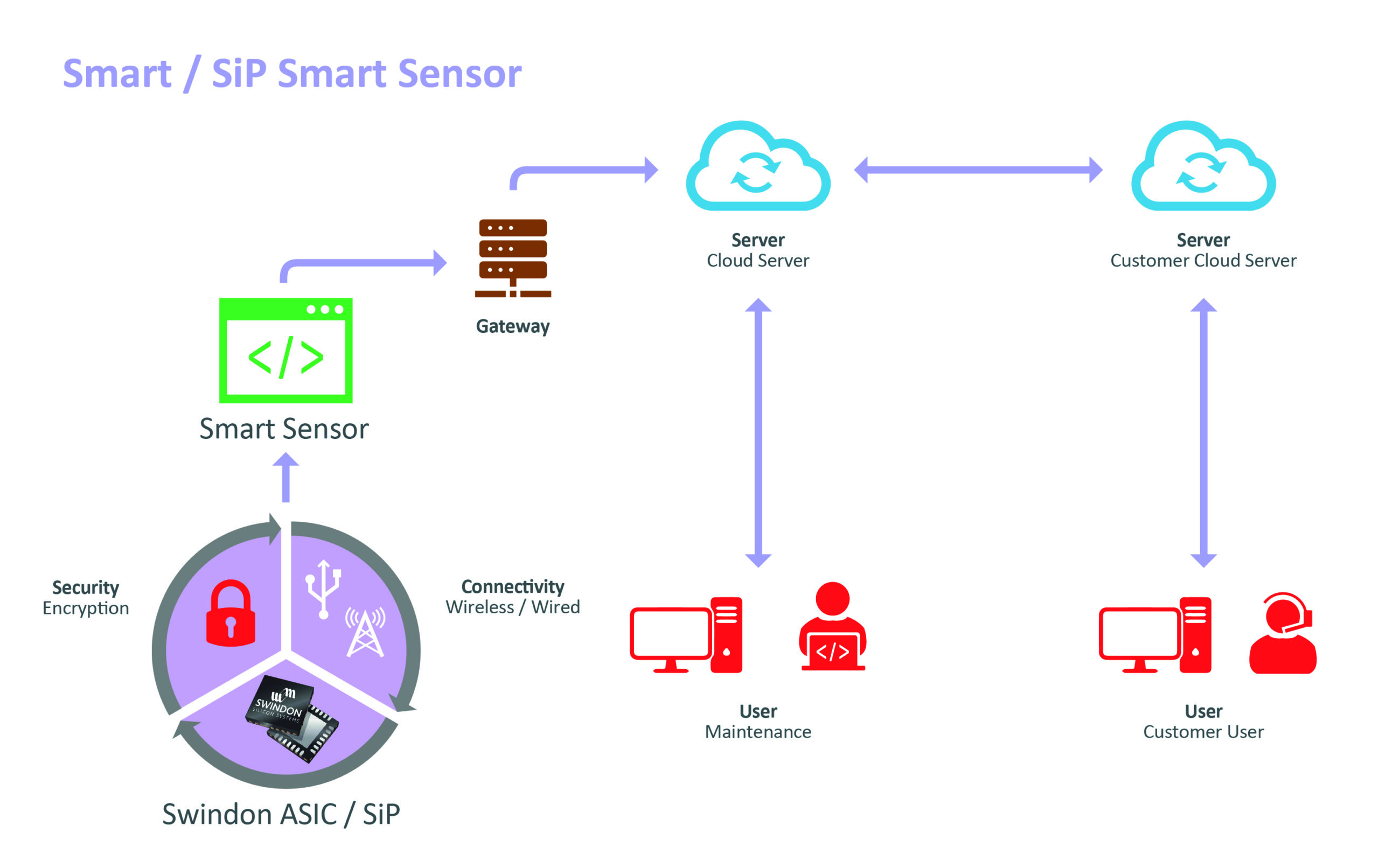
Total Control of the Manufacturing Process
The real benefit of the IIoT to a manufacturing facility is the total control of all aspects of the manufacturing process from materials in, production line precision to the finished product out. This is achieved using various types of networked sensors throughout the manufacturing process flow that collect and interpret the necessary data.
Smart Sensors are the gateway to this automation and Smart Sensor developers are increasingly looking towards ASICs / SiP technology as the enablers that ensure this functionality is both commercially and technically viable.
What are Smart Sensors? Sense, Condition, Communicate
Smart Sensors vary depending upon where they reside in the process and generally receive an input that can be obtained via linear, rotary, pressure, temperature or optical measurement systems, to name just a few. The analogue output signal needs to be conditioned and digitised to allow them to interface with the facility’s computer control systems. Communications between sensors and the network can be via a number of proprietary protocols, either RF or wired.
Smart Sensors in Industry – Key Characteristics
One leading manufacturer of Smart Sensors describes their key characteristics like this:

Analogue Front End
The ability to read and process the signal being received from the sensor

Signal Conditioning
To preserve the integrity of the received signal and enable its onward use

Communication Protocol
The use of a variety of communication standards such as BLE, I/O-Link, Wi-Fi and ZigBee to connect the sensor data with other local users and hubs

Data Processing
Smart Sensors in Industry – Requirements
The requirements for a smart sensor are:
Be able to sense, measure, interpret and communicate
Must be compact and use as little power as possible
Must be commercially viable within the whole system
Find out whether your project fits
An initial discussion will conclude whether your application does, or does not, suit the ASIC or SiP route
Today, it is possible to integrate the required smart sensor functionality into a mixed signal ASIC, using standard CMOS geometries ranging from 55nm to 350nm, depending upon the individual application requirement and the chosen communication protocol. These standard geometries can achieve:
- a high level of digital integration, including digital signal processors and microprocessors
- can accommodate the precision analogue functionality of the design whilst remaining within the performance and cost budget of the device.
The nature of sensing elements has also changed particularly with MEMs (micro-electromechanical systems) which can be integrated in a System in Package (SiP) configuration along with other components in the IIoT chain. .
ASICs and SiPs Bring Many Benefits – Some Not Always Obvious
ASICs are complex devices containing many functions. As well as including the processing, conditioning and communications functions required for sensor interfacing, designers working on today’s IIoT related products and systems find an ASIC will incorporate a number of benefits such as performance, size and cost and others that are not always obvious, such as simplified manufacturing processes.
Incorporating a single, multi-functional device designed specifically for your system/sub-system brings with it many advantages – not only for a new design but also for an established product. Here are some compelling reasons why an Application Specific IC or a SiP makes perfect sense in these budget constrained times.
Short-Term Cost, Long Term Return on Investment
There is a short-term cost associated with ASIC/SiP development however the return on investment is high. By integrating functionality such as the analogue front end, signal processing and IoT connectivity, the overall cost of the final product, both in terms of unit and real estate, is much lower compared to its loaded PCB equivalent. An ASIC/SiP solution delivers higher functionality, fewer components, lower power usage, reduced assembly costs and higher reliability.
All the Required Functionality on a Single Silicon Die or Carrier Package
A mixed signal ASIC/SiP is designed to include a wide variety of both analog and digital functionality necessary for your specific application. The result is a chip that is designed to deliver optimised performance to your exact and unique requirements thus ensuring competitive differentiation.
This can be achieved by integrating your system in an ASIC, which will deliver all the required functionality on a single silicon die or when required, by SiP, where several integrated circuits and sometimes sensors, such as MEMS, preferably at die level, are enclosed in a single carrier package. The individual die may be either stacked or laid adjacent dependent upon the specific requirements.
Full Functionality with Robustness in the Field
ASICs are complex devices containing many functions. Your design team will know most of their system requirements for example, the supply voltages, analog front end, signal processing and communications. Functionalities such as a microprocessors (ARM Cortex for example), memory sizes and types (Flash or EEPROM for example), power management, ADCs, DACs and low and band-pass filtering. Sensors such as MEMS pressure, photodiode and temperature may also be required. Frequency generators and a wide choice of communication protocols, both wireless and wired, might be known but will all need to be considered for the custom design along with security requirements. Device protection is also an important element such as EMC and surge and reverse polarity which provides robustness in the field.
Power Saving
Because of its size and the fact that an ASIC replaces most of a PCB full of components, you can expect much higher efficiency and much lower power consumption.
IP Protection with Full Ownership
One of the principal reasons why a company will commission an ASIC/SiP is to protect its Intellectual Property (IP). The strength of an ASIC is that it is extremely difficult to re-engineer the IC or for it to be “re-used” in other designs. Swindon provides our customers with full ownership of the completed system design ensuring that the IP of our customers remains firmly in their possession.
Non-Obsolescence Guarantee
Customers also choose the ASIC route to guarantee component supply for the lifetime of their product with no gaps in availability. Swindon provides assurances that the device will be available until the customer end of life’s its product manufacture. This is in sharp contrast to a solution built using standard components whose manufacturers readily consign them to the obsolescence bin once the part no longer makes financial sense to the supplier.
The First Step to an ASIC/SiP Solution
An initial contact will satisfy yourself that your application does, or does not, suit the ASIC or SiP route and that the chip supplier understands your requirements and has the expertise and capacity to complete your project. At this initial meeting, both yourself and the supplier need to be satisfied that the project has a future.
Your design team will have a clear idea about the product you are developing, the timescales involved and the available budget. The ASIC development is a well-trodden path and your chosen supplier will be able to provide you with a full breakdown of the project timings and costs at the quotation stage. All aspects of the process flow, development and payment milestones are agreed prior to commencing the project and there should be no hidden costs.
Swindon will quickly show you how its engineering excellence in delivering the latest ASIC / SiP technology will help to differentiate your product from your competition and ensure a commercial and technical advantage.
So, if you are a developer of Smart Sensors or industrial systems or sub systems that you believe could benefit from higher integration along with IoT connectivity then why not contact Swindon for a confidential discussion to discuss what it is you are trying to achieve and how Swindon’s ASIC/SiP technology could help you realise it.